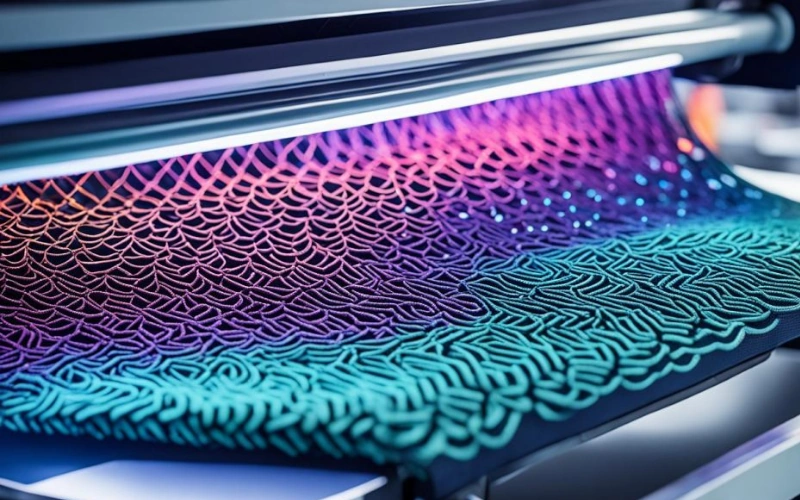
3D printing, also known as additive manufacturing, is an innovative process that creates physical objects by layering materials based on digital designs. Originally developed in the 1980s, it has now evolved into a versatile technology used across multiple industries, from automotive to healthcare, fashion, and even aerospace. In this article, we’ll explore the basics of 3D printing, its types, applications, and how it continues to shape the future of manufacturing and design.
Table of Contents
How 3D Printing Works
At its core, 3D printing involves transforming a digital design file into a tangible object. This process begins with 3D modeling software or computer-aided design (CAD) files, which are then sliced into digital layers. The printer builds the object layer by layer, using materials like plastic, metal, or even bio-materials, until the final structure is complete. Unlike traditional subtractive manufacturing, which removes material to create a form, 3D printing adds material only where necessary, resulting in reduced waste.
Types of 3D Printing Technologies
Several types of 3D printing technologies are popular today, each suited for different applications and materials:
- Fused Deposition Modeling (FDM): The most common 3D printing method, FDM, extrudes melted thermoplastic layer by layer. It’s popular for its affordability and is often used in prototyping.
- Stereolithography (SLA): This process uses a laser to cure liquid resin into hardened plastic. SLA is renowned for producing high-resolution, detailed prints, making it suitable for dental and medical applications.
- Selective Laser Sintering (SLS): Using a laser to fuse powder materials (like nylon or polyamide), SLS produces durable, complex parts and is widely used for industrial manufacturing.
- Digital Light Processing (DLP): Similar to SLA, DLP uses a light source to harden resin, offering rapid printing speeds and precise detailing. It’s popular in jewelry and high-resolution prototypes.
- Metal 3D Printing (DMLS and SLM): Direct Metal Laser Sintering (DMLS) and Selective Laser Melting (SLM) fuse metal powder to produce fully dense metal parts. These are often used in aerospace and automotive sectors.
Applications of 3D Printing
3D printing’s versatility has unlocked a myriad of applications, including but not limited to:
- Healthcare and Medical Devices: 3D printing is revolutionizing healthcare by enabling customized prosthetics, implants, and even bioprinted tissues. It provides affordable solutions tailored to each patient, leading to higher compatibility and comfort.
- Aerospace and Automotive: The aerospace and automotive sectors use 3D printing for lightweight, high-strength parts. It allows rapid prototyping, custom parts production, and on-demand manufacturing, all of which help reduce costs and development times.
- Architecture and Construction: In architecture, 3D printing enables the construction of complex models and structures. The construction industry is exploring large-scale 3D printing for buildings, creating sustainable homes more quickly and affordably than traditional methods.
- Consumer Goods and Fashion: 3D printing is making waves in the fashion industry, allowing for personalized jewelry, accessories, and even clothing. In consumer goods, 3D printing aids in creating prototypes, custom-designed products, and replacements for discontinued parts.
- Education and Research: 3D printing in education offers hands-on learning for students and researchers, allowing them to explore engineering, design, and scientific concepts. It’s also an essential tool in research and development, enabling rapid experimentation with complex models.
Advantages of 3D Printing
3D printing brings several advantages that make it indispensable in many fields:
- Customization: 3D printing offers unparalleled flexibility in customizing products for individual needs, especially valuable in medical prosthetics and wearable items.
- Efficiency and Speed: Prototyping and manufacturing processes are significantly faster, reducing the time required to bring products to market.
- Cost Savings: With on-demand production and less waste generated, 3D printing can reduce material costs and eliminate the need for large storage spaces.
- Sustainability: Since only the needed material is used, additive manufacturing is often more environmentally friendly than traditional methods.
Challenges and Future of 3D Printing
While 3D printing offers immense potential, it does face challenges:
- Material Limitations: The types of materials available for 3D printing, especially biodegradable or biocompatible options, are still limited, which can restrict applications.
- Cost of Equipment: Although 3D printing has become more accessible, high-end printers are still costly and require maintenance, which may limit access for small businesses.
- Quality Control: Ensuring consistency and quality across large batches remains a challenge, particularly in industries where precision is critical.
Despite these challenges, advancements in 3D printing technology continue to push boundaries. In the coming years, we can expect the development of faster, more affordable, and environmentally friendly printers. Industries may increasingly use hybrid manufacturing—combining traditional and additive methods—allowing for the creation of even more complex and customized products.
Conclusion
3D printing has grown from a niche prototyping tool into a transformative technology reshaping industries and democratizing manufacturing. Its ability to produce complex designs with precision, efficiency, and customization holds promise for a more sustainable and innovative future. As we continue to refine the technology and expand material options, 3D printing’s potential impact will only grow, paving the way for new breakthroughs and creative possibilities in the world of design, engineering, and beyond.